De store bilfabrikker arbejder målrettet og
intensivt på elektrisk mobilitet. BMW er med i front
og satser ikke alene på, at bygge miljørigtige
premium-biler, men også at gøre dette på en
miljørigtig måde. Man kan tale om bæredygtig
bilproduktion i yderst konsekvens.
Dette arbejde inkluderer naturligt det begreb, der
kaldes ”connected cars”, altså biler, der ikke bare
kommunikerer via internet og for den sags skyld et
hvilket som helst netværk, på ejeren eller brugerens
kommando, men automatisk kommunikerer med den
relevante omverden for i sidste instans, at lette
mobiliteten for brugeren og ikke mindst, at gøre
dette på en bæredygtig acceptabel måde.
BMW fabrikken i Leipzig
BMW’s elektriske hotspot ligger i Leipzig i den
sydøstlige del af Tyskland, her finder produktionen
af de såkaldte ”i” biler sted, aktuelt kører 20.000
BMW i3 biler om året plus en håndfuld af den potente
sportsvogn, i8 ud af det miljøoptimerede samlebånd.
Men produktionen og udviklingssamarbejdet er spredt
ud til de centre, der er eksperter i enkelt
elementer, der indgår i forløbet, og kapaciteten er
så fleksibel, at den kan udbygges i takt med at
markedet er parat til at aftage flere biler.
Eksempelvis produceres de karbonfiber dele, som
monocoquen hovedsagelig er fremstillet af, i et
forløb, hvor man starter i Moses Lake i staten
Washington i USA og siden færdiggør elementerne på
en fabrik Wackersdorf i Sydtyskland, inden det
egentlige samlearbejde finder sted i Leipzig.
På besøg i de ”hellige haller”
Vi har besøgt BMW fabrikken i Leipzig og fik et
unikt indblik i den proces og det forløb, der ligger
bag en moderne bæredygtig produktion af miljørigtige
biler. Det er en kontinuerlig proces, som
fremadrettet også vil inkluderer autonome, altså
selvkørende, biler.
BMW i3 er fabrikkens første og hidtil eneste
elektrisk drevne bil. I modsætning til flere andre
bilproducenter har man nemlig valgt, at udvikle i3
helt fra bunden som en elektrisk bil, og man har
haft klare mål om, at bilens samlede livsforløb
skulle belaste miljøet mindst muligt.
Den store hurdle for elektriske biler, som i øvrigt
forventes at blive mindre og mindre i de kommende
år, er begrænsningen i rækkevidde. En vigtig
rækkeviddeforlængende faktor er bilernes vægt. Men
vægtreduktion må ikke ske på bekostning af bilens
sikkerhed og køreegenskaber. Derfor er en BMW i3 i
vidt omfang skabt i karbonfiber – eller mere præcist
karbonfiber forstærket polymer, eller i daglig tale
”kulfiberforstærket plastic”.
Bæredygtig produktion
Et sådan materiale har hidtil fortrinsvist været
anvendt i flyindustrien og til produktion af
racerbiler og eksotiske sportsvogne. Materialet er
meget let, det er meget stærkt og stift og derfor
ideelt til at skabe lette biler med gode
køreegenskaber. Men produktionen af materialet er
meget energikrævende – og kostbart. Fibrene, som er
7/1000 millimeter tykke og minder lidt om meget
tynde silketråde, består stort set kun af kul. De
flettes populært sagt sammen i en stabil grafit
struktur og siden indgår de, lag på lag, på kryds og
tværs i de færdige elementer, som f.eks. kan udgøre
siden af en BMW i3.
Et sådan sideelement med færdige huller til
hjulkasser, ruder osv. fra den ene ende til den
anden vejer eksempelvis kun omkring 10 kg. De limes
og skrues siden sammen som et bedre modelbils
plastic byggesæt og resultatet bliver en selvbærende
såkaldt monocoque, hvorpå drivlinen, hjul, styretøj,
sæder, ruder, interiør og ikke mindst de ydre
plastic elementer fastgøres. Præcis samme teknologi
anvendes til produktion af f.eks. de Formel E
racerbiler, som BMW netop har inkorporeret i
fabrikkens udviklingsprocesser.
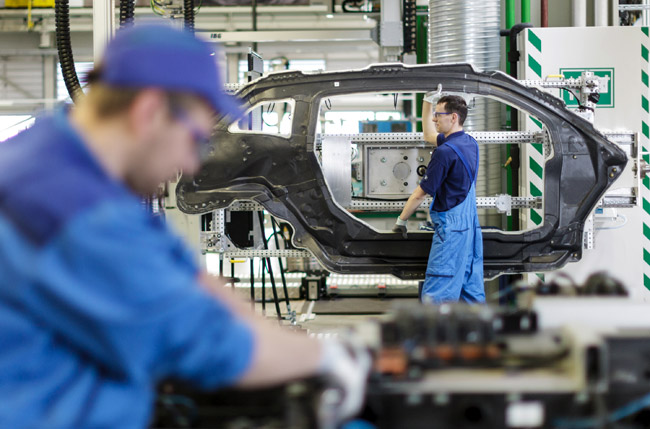
Side-elementerne til i3 monocoquen håndbæres fra
transportkassen til samlebåndet - det vejer kun 10
kg.
Vedvarende energi
Man har valgt indtil videre at fabrikere kulfiberen
i Moses Lake hos firmaet SGL Automotive Carbon
Fibers (ACF), som delvist ejes af BMW, fordi man dér
er eksperter i med mindst mulig belasting af miljøet
at skabe det værdifulde materiale. Trods den store
energianvendelse er fabrikkens produktion
fuldstændig CO2 fri, fordi al energien stammer fra
vedvarende, lokalt frembragt hydroelektrisk kraft.
Dermed er den eneste miljøforurening den, der er
forbundet med at transportere delene til Tyskland.
I Wackersdorf har ACF også en fabrik, som med stor
ekspertise bearbejder kulfiberen til de færdige
elementer, der siden bringes til samlebåndet i
Leipzig, som er 100 procent BMW-ejet.
På samme fabrik produceres flere andre BMW-modeller,
men til forskel for de konventionelle biler er
i3-samlebåndet kun 110 meter langt – det er cirka en
tredjedel af det, der benyttes til konventionelle
biler. Det har man opnået ved at medtage tankegangen
om bæredygtighed i produktionsprocessen.
Produktionen er naturligvis 100 procent
computerstyret, men der indgår også manuel
detailstyring, udført af fabrikkens personale i de
enkelte samlingsprocesser.
Link til importøren
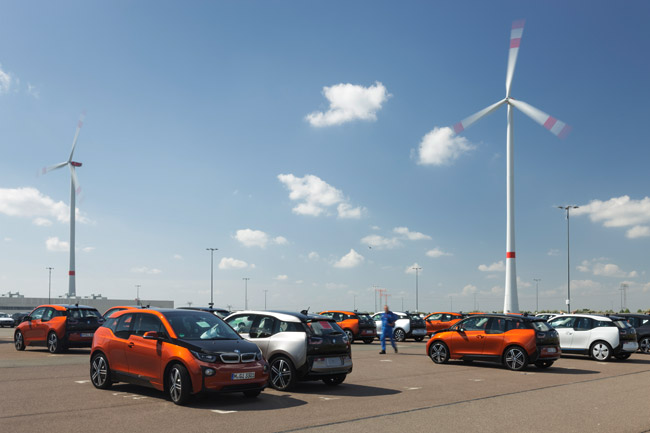
Energien
på den moderne BMW fabrik i Leipzig leveres så vidt
muligt af vindkraft fra fabrikkens foreløbig fire
200 meter høje vindmøller, der er udstyret med 2,5
mW turbiner. |